MicroShield Coating
MicroShield SMT Stencil Coating Technology
The stencil industry faces the challenge of producing smaller electronics at a faster pace, all while maintaining affordability. These demands create a dilemma between electronic miniaturization and cost efficient production.
Traditional stencil treatments tend to can increase cycle time and yields, leading to a decrease in overall production output and efficiency. The application process is extended due to the need to run stencils through distilled water to ensure its surface is water break free.
Stencil wipes, although convenient, are an overabundance of product. Whether thrown away or left laying inside of a container, waste of product materials is higher, ultimately resulting in unnecessary costs.
MicroShield coating transforms the efficiency of on-contact hydrophobic coatings in the SMT stencil field. The coating’s unique chemical composition allows it to be hand-applies to solder paste stencils and create a variety of properties.
This innovative technology reduces cycle times and improves overall production yields by eliminating the need to be rinsed off or thoroughly dried upon application. Therefore, unlike conventional coating treatments, MicroShield accommodates cost and usability demands.
Customers have full control of how the coating is applies, as it is an on-contact stencil coating. MicroShield’s easy-to-use bottle makes it possible to allocate the exact amount of coating onto its applicator. This incredible extent of control ensures that users will never waste a single drop during application, making MicroShield the perfect cost-effective coating for small production lines and prototyping.
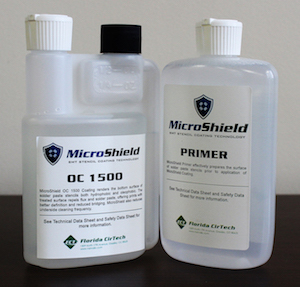
Application
Remove any contamination from surface.
Apply 7ml of the MicroShield Cleaner / Primer in a circular motion.*
*Note: it is not necessary to run stencils underwater or use an air gun to dry.
Next, apply 7ml of the MicroShield coating on a lint-free cloth. Coat in circular and vigorous patterns until the cloth is dry.
Lastly, let it cure for 2 minutes. Then buff with another dry lint-free cloth for 90 seconds. An electric palm buffer can help with this process.